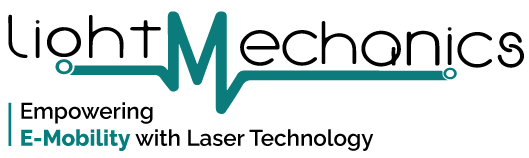
Want to explore the laser technology best suited for your application? Send us your samples for a FREE trials!
Contact us nowStator and Rotors are a key part of the Electric Vehicle motor and are made of hundreds of laminated and joined thin electrical steel sheets. These electrical steel sheets are designed to be thin (0.2, 0.27 or 0.5 mm) to obtain high magnetic permeability and low iron loss.
The laminated electrical sheets needs to be welded at the external circumference to enhance its mechanical strength. Excellent Joint strength and magnetic properties are two of the most important performance indicators of the stator.
Researchers compared the current fusion welding methods (Tig vs Laser) to analyze microstructure, mechanical performance, residual stress and magnetic properties of the electrical steel laminations, where laser was welding was found to be more superior.
Due to larger heat input, the geometry size of the weld beam in TIG welding is larger than that in laser welding, which leads to higher tensile shear strength.
But Laser is considered be one of the most potential and reliable welding methods to obtain high quality laminations due to:
The eddy current loss in TIG-welded laminations is larger than that in laser-welded laminations because of the larger connection area between the laminations.
The magnitude of the residual stress in TIG-welded laminations was also larger than that in laser-welded laminations, which led to severe degradation of the hysteresis property.
To conclude, the heat input in laser welding is much more concentrated and controllable than that of TIG, and laser should be a better heat source for high quality welding of the electrical steel laminations due to its capability to deliver high welding speed and stable quality.